In industries where precise heat application is critical, the term PTFE-coated heat platen frequently emerges. But what is a PTFE-coated heat platen, and why is it so important across various industries? This article explores the concept, its applications, benefits, and maintenance tips to provide a comprehensive understanding of this essential tool.
What is a Heat Platen?
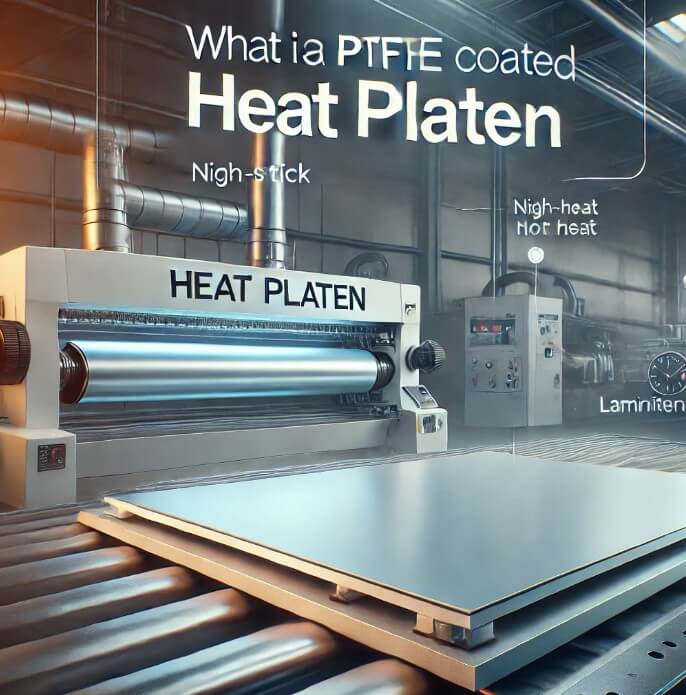
A heat platen is a flat, heated surface commonly found in equipment like heat presses, laminators, and industrial sealing machines. Its primary function is to apply consistent heat and pressure to a material or substrate. Heat platens are integral to processes like:
- Sublimation printing to transfer vibrant designs onto fabrics.
- Heat transfer of vinyl onto textiles.
- Sealing and laminating in packaging.
When coated with PTFE, the platen becomes even more versatile and efficient.
What is PTFE and Why Is It Used?
PTFE (Polytetrafluoroethylene) is a synthetic material known for its non-stick, durable, and heat-resistant properties. Commonly recognized by its brand name Teflon, PTFE is used as a coating to enhance the functionality of heat platens.
Key Properties of PTFE:
- Non-stick Surface: Prevents materials like adhesives and inks from sticking.
- High Heat Resistance: Performs well under extreme temperatures.
- Durability: Resists scratches, corrosion, and wear over time.
- Low Friction: Materials glide smoothly over its surface.
Features of a PTFE Coated Heat Platen
A PTFE-coated heat platen combines the heating efficiency of a traditional platen with the added advantages of PTFE coating. Key features include:
- Even Heat Distribution: Ensures uniform heating across the entire surface.
- Non-stick Coating: Reduces residue buildup, enhancing productivity.
- Ease of Cleaning: Residue or adhesives can be wiped off effortlessly.
- Long Lifespan: The durable PTFE layer protects the platen from wear and tear.
Applications of PTFE Coated Heat Platens
PTFE-coated heat platens are used across diverse industries due to their versatility. Below are some notable applications:
1. Textile Printing and Heat Transfer
- Used in sublimation printing to transfer vibrant designs onto fabrics.
- Ensures smooth application of heat transfer vinyl (HTV) without sticking or smudging.
2. Industrial Sealing and Laminating
- Laminating materials like wood, paper, or plastic.
- Sealing food packaging to ensure air-tight closures.
3. Composite Forming
- In automotive and aerospace industries, PTFE-coated platens are used for forming composites due to their non-stick properties and high heat resistance.
4. Food Processing
- Essential in machines that heat-seal food packaging, ensuring hygiene and precision.
Advantages of Using PTFE Coated Heat Platens
PTFE-coated heat platens offer significant benefits, including:
- Improved Efficiency: The non-stick surface reduces downtime caused by residue buildup.
- Consistent Results: Even heat distribution ensures high-quality output.
- Versatility: Suitable for various materials and industrial processes.
- Reduced Maintenance: The PTFE coating resists scratches and wear, minimizing maintenance needs.
- Cost-Effectiveness: The durability of PTFE extends the platen’s lifespan, saving replacement costs.
Regular vs. PTFE Coated Heat Platens
Feature | Regular Heat Platen | PTFE Coated Heat Platen |
---|---|---|
Non-stick Surface | No | Yes |
Heat Resistance | Moderate | High |
Ease of Cleaning | Difficult | Easy |
Durability | Prone to scratches | Resistant |
Applications | Limited | Versatile |
Maintenance Tips for PTFE Coated Heat Platens
To ensure the longevity and performance of your PTFE-coated heat platen, follow these maintenance tips:
- Regular Cleaning: Wipe the surface with a soft, damp cloth to remove residue after use.
- Avoid Abrasives: Never use sharp tools or abrasive materials that may damage the coating.
- Temperature Control: Do not exceed the recommended operating temperature to maintain the integrity of the PTFE layer.
- Periodic Inspection: Check for signs of wear or scratches and replace the coating if necessary.
FAQs
1. What is the purpose of a heat platen?
A heat platen applies consistent heat and pressure for processes like heat transfer, laminating, and sealing. When coated with PTFE, it adds non-stick and durability features.
2. Why is PTFE used for coating heat platens?
PTFE is used for its non-stick, heat-resistant, and durable properties, which enhance the functionality and lifespan of heat platens.
3. In which industries are PTFE-coated heat platens used?
These platens are commonly used in textiles, packaging, food processing, automotive, and aerospace industries.
4. How do I clean a PTFE-coated heat platen?
Use a soft, damp cloth to wipe the surface. Avoid using harsh chemicals or abrasive tools to maintain the PTFE coating.
5. Can PTFE-coated platens withstand high temperatures?
Yes, PTFE-coated platens are designed to handle high temperatures without degrading, making them suitable for industrial applications.
6. What is the lifespan of a PTFE-coated heat platen?
With proper maintenance, a PTFE-coated heat platen can last for several years, depending on usage and care.
7. Are PTFE-coated heat platens cost-effective?
Yes, their durability and low maintenance requirements make them a cost-effective choice in the long run.
Conclusion
A PTFE-coated heat platen is an indispensable tool for industries requiring precise and efficient heat application. Its non-stick surface, durability, and versatility make it a superior choice over regular heat platens. Whether in textile printing, food processing, or industrial sealing, these platens deliver consistent results and long-lasting performance. By understanding their features, applications, and maintenance, you can maximize their benefits and ensure seamless operations in your processes.
For more topics visit OutlineTips.